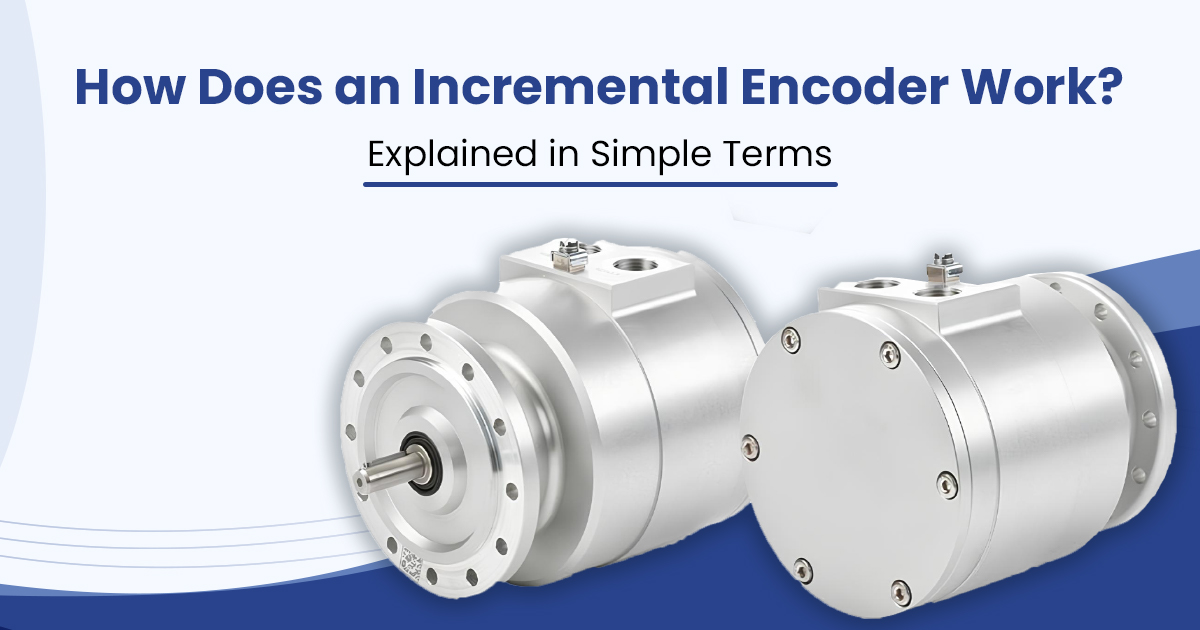
How Does an Incremental Encoder Work? Explained in Simple Terms
- May 19, 2025
- by
- bhavik@bcreative.in
Have you ever wondered how machines keep track of their movement or position without getting lost in the process? That’s where incremental encoders come into play. Whether in offshore applications, the chemical industry, or stainless steel housing, these small devices play a big role in precise motion control. But how do they actually work?
Let’s break it down.
What Is an Incremental Encoder?
An incremental encoder is a sensor that tracks how far a shaft turns, how quickly it moves, and which way it’s turning. In contrast with absolute encoders, which provide a set position value, incremental encoders provide a sequence of pulses as the shaft rotates. These pulses are counted to calculate movement.
They lose their position when power is removed. Whenever the machine restarts, the encoder resets to zero. This makes them a practical choice for setups where real-time tracking is more important than knowing the exact position at all times.
Understanding Incremental Encoders
Every incremental encoder contains a rotating disc that is connected to a shaft. This disc has alternating transparent and opaque lines arranged around it. As the disc spins between a light source and a sensor, these lines block and transmit light in a repetitive pattern. This pattern of light and dark is turned into electrical pulses that the system can read.
Incremental encoders usually provide three outputs:
➡️Channel A – The main pulse signal
➡️Channel B – A second pulse signal, shifted slightly in timing from A (used for direction)
➡️Channel Z – A single pulse for each full revolution (used as a reference point)
By counting these pulses and observing their sequence, machines can track how far and in which direction the shaft has rotated.
Reading Incremental Encoders
Reading an incremental encoder means processing its output signals to determine motion. This is typically done by a controller or PLC.
➡️The pulse count from Channel A tells how much movement has occurred.
➡️The timing of signals between Channel A and Channel B determines the direction of rotation.
➡️The Z channel gives one pulse per full rotation and is used to mark or reset the position.
For example, if Channel A comes before Channel B, it means the shaft is turning in one direction. If Channel B leads Channel A, it’s turning the opposite way. This method helps systems know not just how far something has moved but also where it’s headed.
Where Are Incremental Encoders Used?
You’ll find them in a wide range of machinery and systems:
- Offshore Applications
- Chemical Industry
- Stainless Steel Housing
- Rolling Mills
- Crane Systems
They’re commonly chosen for these jobs because they provide fast and accurate feedback without too much complexity.
Different Types of Encoders
Encoders generally fall into three main categories:
- Incremental – Tracks movement using pulses
- Absolute – Provides a unique code for each position
- Linear – The device measures motion along a straight path rather than rotational movement.
Each type fits different needs, depending on how much detail or positioning memory the system requires.
Incremental encoders are best for many industrial tasks. They deliver consistent performance, work well with motion control systems, and are easy to integrate. If you’re working with equipment that needs speed tracking or direction detection, they’re a solid choice.
Not sure which encoder suits your setup? Contact us at Emco Precima for any support and inquiry for regarding incremental encoders.
FAQs
What Is an Incremental Encoder?
An incremental encoder measures changes in position or speed instead of absolute position.
What exactly does an incremental encoder do?
It measures how much a rotating shaft turns and in which direction. It sends out pulses as the shaft moves, which helps the system track speed and position.
Where are incremental encoders used?
Incremental encoders are used in numerous applications requiring position or speed feedback, especially in industrial or heavy-duty applications.
How are incremental encoders different from absolute encoders?
An incremental encoder resets to zero when the power goes off. It only tracks movement from that point forward. An absolute encoder, on the other hand, always knows its position, even after the machine is restarted.
What are the three types of encoders?
The three main types of encoders are linear, rotary, and angle encoders.
What makes sine encoders and incremental encoders different?
Sine encoders send smooth, analog signals and are used where very fine movement needs to be tracked. Incremental encoders send digital pulses and are more commonly used in industrial equipment.
What is the principle of an encoder?
An encoder reads movement and turns it into electrical signals. These signals help the machine understand position, direction, and speed.